Сварка давлением
К сварке давлением относятся различные способы сварки, при которых соединяемые детали сжимаются механическим усилием, за счет чего достигаются сплошность и прочность соединения.
В подавляющем большинстве случаев сварка давлением осуществляется с подогревом свариваемых деталей тем или иным способом и лишь в отдельных специальных случаях сварка достигается без нагрева (например, холодная сварка, сварка взрывом). Из всех способов сварки давлением наибольшее распространение получила электрическая контактная сварка.
Машина контактной сварки
Контактной сваркой или сваркой сопротивлением называется способ электрической сварки, при котором нагрев осуществляется за счет преимущественного выделения теплоты в местах соприкосновения свариваемых деталей при протекании через них электрического тока (рис. 1).
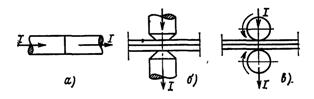
Рис. 1. Основные разновидности контактной сварки: а - стыковая, 6 - точечная, в - роликовая, I - направление сварочного тока.
Для контактной сварки характерна местная концентрация тепловой мощности и, следовательно, высокой температуры в области стыка свариваемых деталей, что обусловливается значительным сопротивлением контакта стыка в сравнении с сопротивлением самих деталей. В этом отношении контактная сварка является весьма экономичным и целесообразным видом сварки.
Контактная сварка может осуществляться как на постоянном, так и на переменном токе, однако на практике применяется почти исключительно переменный ток, так как необходимые для сварки токи порядка тысяч и даже десятков тысяч ампер при напряжениях в несколько вольт могут быть наиболее просто получены при помощи трансформаторов, специальные источники постоянного тока для этой цели были бы слишком дороги, сложны в изготовлении и менее надежны в эксплуатации.
Стыковая сварка
При стыковой сварке торцы соединяемых деталей приводятся в соприкосновение, после чего вдоль деталей пропускается значительный ток, разогревающий место стыка до необходимой для сварки температуры. Затем продольным сжимающим усилием достигается непосредственная сплошность соединения.
Различают две разновидности стыковой сварки: сварку без оплавления (сварку сопротивлением) и сварку с оплавлением.
При сварке сопротивлением детали с обработанными торцами приводятся в соприкосновение и сжимаются значительным усилием, затем через детали пропускается ток и за счет контактного сопротивления в месте стыка возникает концентрированное выделение теплоты.
После достижения в зоне стыка необходимой для сварки температуры под влиянием сжимающего усилия осуществляется пластическая сварка соединяемых деталей. По окончании цикла сварки ток выключают, а затем снимают сжимающее усилие.
Сварка сопротивлением обычно производится при плотности тока 5 - 10 кА и удельной мощности 10 - 15 кВА на 1 см2 поперечного сечения свариваемых деталей. Эта разновидность сварки, как правило, применяется для соединения деталей небольшого поперечного сечения (приблизительно до 300 мм2).
При стыковой сварке с оплавлением нагрев деталей проводят в три или две последовательные стадии - предварительный подогрев, оплавление и окончательная осадка или только в две последние стадии.
В начальный момент сварки осуществляется контакт свариваемых деталей усилием сжатия 5 - 20 МПа. После этого включают ток, который разогревает места стыка до 600 - 800 °С (для стали), так же, как при стыковой сварке без оплавления. Затем сжимающее усилие снижают до 2 - 5 МПа, вследствие чего увеличивается сопротивление контакта и соответственно снижается сварочный ток.
При ослаблении сжатия уменьшается действительная площадь касания торцов деталей, ток устремляется в ограниченное число точек соприкосновения и нагревает их до температуры плавления, а при дальнейшем нагревании в этих условиях в отдельных точках происходит перегрев металла до температуры парообразования.
Под влиянием избыточного давления пары металла вырываются из зоны сварочного контакта наружу и вытесняют в воздух частицы жидкого металла в виде веера искр, а часть расплавленного металла стекает каплями вниз. За разрушенными выступами соприкасаются между собой очередные выступы контакта, создавая новые пути для сварочного тока с повторением указанного эффекта.
Такой процесс последовательного оплавления концов деталей по элементарным выступам продолжается до тех пор, пока торцы свариваемых деталей не покроются сплошной пленкой полужидкого металла, после чего относительно небольшим усилием осадки создается металлическая сплошность свариваемого стыка. При этом избыточное количество расплавленного металла выдавливается из контакта в виде грата (венчика).
Нагрев выступающих концов свариваемых деталей осуществляется главным образом теплопроводностью от сварочного контакта, где температура имеет наибольшее значение. Нагрев деталей между стыком и токоподводящими электродами за счет протекающего тока в процессе оплавления весьма незначителен.
Регулирование количества подводимой энергии при заданном сопротивлении контакта, определяемом условиями сварочного процесса, может осуществляться либо изменением сварочного тока, либо изменением продолжительности протекания тока.
Принцип действия машины для стыковой сварки иллюстрирует рис. 2.
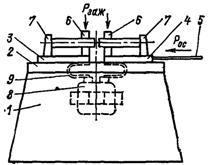
Рис. 2. Схема машины для стыковой сварки: 1 - станина, 2 - направляющие, 3 - неподвижная плита, 4 - подвижная плита, 5 - подающее устройство, 6 - зажимное устройство, 7 - упоры, 8 - трансформатор, 9 - гибкий токоподвод, Рзаж - усилие зажима изделий, Рос - усилие осадки изделий.
Машины для стыковой сварки классифицируются следующим образом.
1. По способу сварки - для сварки сопротивлением и оплавлением (непрерывным оплавлением нли оплавлением с подогревом).
2. По назначению - универсальные и специализированные.
3. По устройству механизма подачи - с пружинным, рычажным, винтовым (от штурвала), пневматическим, гидравлическим или электромеханическим приводом.
4. По устройству зажимов - с эксцентриковыми, рычажными и винтовыми зажимами, причем рычажные и винтовые зажимы могут выполняться либо ручными, либо механизированными с пневматическим, гидравлическим или электромеханическим приводом.
5. По способу монтажа и установки - стационарные и переносные.
Точечная сварка
При точечной сварке соединяемые детали обычно располагаются между двумя электродами, закрепленными в специальных электрододержателях. Под действием нажимного механизма электроды плотно сжимают свариваемые детали, после чего включается ток.
За счет прохождения тока свариваемые детали быстро нагреваются до температуры сварки, причем наибольшее выделение теплоты имеет место на соединяемых поверхностях, где температура может превышать температуру плавления свариваемых деталей.
На рис. 3 показано распределение температур по сечению свариваемых деталей, характерное для конечной стадии сварки стали.
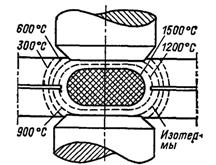
Рис. 3. Температурное поле в конечной стадии точечной сварки
Наиболее высокая температура имеет место в центральной заштрихованной части сварной точки - ядре. Поверхность соприкосновения свариваемой детали с электродом (обычно водоохлаждаемым) нагревается до сравнительно невысокой температуры, однако при наличии жидкого или полужидкого ядра и прилегающего к ядру пластичного металла усилие прижима электродов вызывают вмятины на поверхности свариваемых деталей.
Температура в ядре сварной точки обычно несколько превосходит температуру плавления металла. Диаметр расплавленного ядра определяет диаметр сварной точки, обычно равный диаметру контактной поверхности электрода.
Время сварки одной точки зависит от толщины и физических свойств материала свариваемых деталей, мощности сварочной машины и сжимающего усилия. Это время колеблется от тысячных долей секунды (для весьма тонких листов из цветных металлов) до нескольких секунд (для толстых стальных деталей). Для грубой оценки время сварки одной точки малоуглеродистой стали можно принять равным 1 с на 1 мм толщины свариваемого листа. Скорость нагрева металла до температуры сварки существенно зависит от интенсивности выделения теплоты.
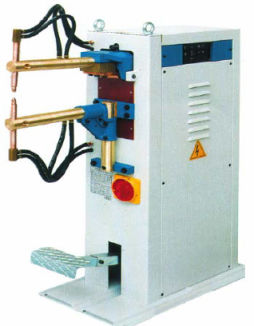
Машина точечной сварки
Роликовая сварка
При этом виде сварки соединение деталей непрерывным или прерывистым швом осуществляется за счет пропускания через свариваемые детали тока, подводимого посредством вращающихся роликов (рис. 4).
Рис. 4. Принцип роликовой сварки: 1 - сварочный трансформатор, 2 - роликовые электроды, 3 - привод вращения роликов, 4 - свариваемые детали
По характеру процесса роликовая сварка аналогична точечной. Роликовую сварку часто называют шовной, что, строго говоря, неправильно, так как понятие шовной сварки может быть распространено практически на все виды сварки.
Машины для роликовой сварки обычно снабжены двумя токоподводящими роликами, из которых один выполняется приводным, а другой вращается за счет трения при передвижении свариваемых деталей.
Роликовую сварку чаще всего применяют для соединения тонкостенных деталей, например при изготовлении топливных баков и бочек для транспортировки различных материалов.
Различают три режима роликовой сварки.
1. Непрерывное движение свариваемых деталей относительно роликов с непрерывной подачей тока. Этот метод применяется при сварке деталей суммарной толщиной не более 1,5 мм, так как при больших толщинах выходящий из под роликов стык, будучи в пластическом состоянии, может нарушиться за счет расслоения. Помимо того, при непрерывной подаче тока имеет место значительное коробление свариваемых деталей.
2. Непрерывное движение свариваемых деталей относительно роликов с прерывистой подачей тока. Этим наиболее распространенным методом получают швы с небольшим короблением изделий при меньшем расходе электроэнергии.
3. Прерывистое движение свариваемых деталей относительно роликов с прерывистой подачей тока (шаговая сварка).
Роликовая сварка весьма эффективна при изготовлении тонкостенных сосудов, при производстве сварных металлических труб и ряда других изделий.
Основными элементами роликовых машин являются станина, верхняя и нижняя консоли с роликовыми электродами, механизм сжатия, привод вращения ролика и сварочный трансформатор с гибким токоподводом
Трансформаторы роликовых машин работают в напряженном режиме с ПР = 50 - 60%, что вызывает необходимость усиленного охлаждения их обмоток.
Машины роликовой сварки разделяются: по характеру монтажа - на стационарные и передвижные, по назначению - на универсальные и специализированные, по расположению роликов относительно фронта машины - для поперечной сварки, для продольной сварки и универсальные с возможностью перестановки роликов, о расположению роликов относительно изделия - с двусторонним и односторонним расположением, по способу вращения роликов - с приводом на один ролик, с приводом на оба ролика, с одним верхним роликом, перемещающимся по неподвижной консоли, и с одним роликом и перемещающейся нижней оправкой, по устройству механизма сжатия - на рычажно-пружинные, с приводом от электродвигателя, пневматические и гидравлические, по количеству роликов - на однороликовые, двухроликовые и многороликовые.
Мощность наиболее распространенных роликовых машин обычно составляет 100 - 200 кВА. Аналогично точечной роликовая сварка тонких деталей может выполняться импульсами тока разрядки конденсаторов, для чего выпускаются различные типы роликовых машин.